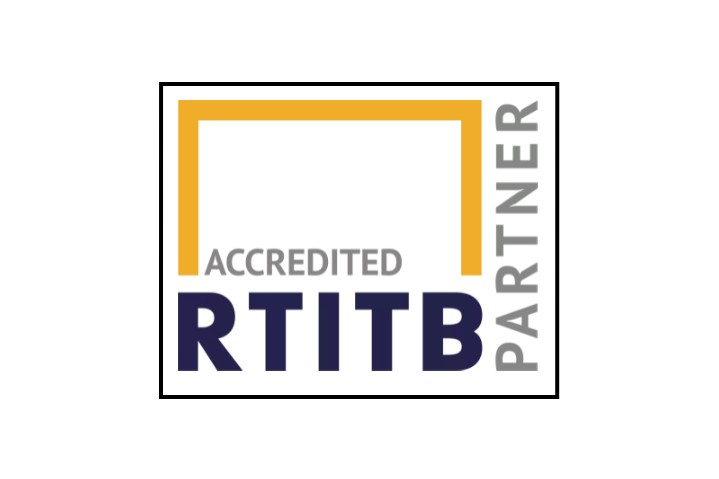
RTITB’s Useful Lift Truck Training Guide
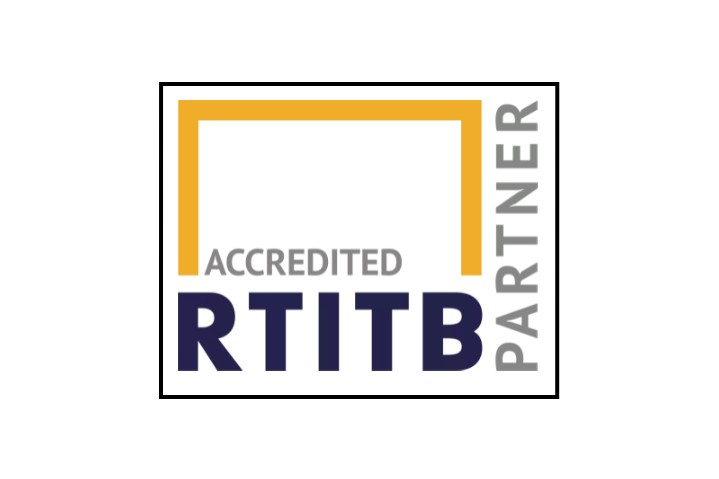
RTITB’s Useful Lift Truck Training Guide
As a proud partner of RTITB, we’ve got access to some of the finest training materials in our industry, so we are delighted to share with you this extremely useful guide they have produced for all businesses where lift trucks are in operation.
This simple guide explains that there are several steps to ensuring safe and efficient operations using lift trucks and enables you to check that you have everything in place to ensure your operators are skilled correctly, and that your business is compliant.
RTITB Lift Truck Training Guide
Safe and skilled operators result in a reduction in operation costs, so you can improve safety for your staff and save money at the same time.
Common misconceptions.
A lot of businesses think that once they have trained their operators on how the truck works, then they are ready to start operating on site.
However, there are 3 stages to this training, and if your training was carried out by an external training provider like us, then the second and third stages are often missed.
You must carry out specific job training, which enables the operator to learn the specifics about the trucks you have on site, and you must then carry out familiarisation training, which enables the operator to try out live work under supervision in your own premises.
Then and only then should your business issue them an Authorisation to operate. This is a formal record of the stages of training your operators have gone through and the operations they are able to undertake in your business.
The guide explains all of this in detail and will point you to further information if you need it. And it also explains the three types of training that are required after your initial training.
If you are interested in our wide range of lift truck training courses for your operators, then please click here for more information.
We hope this resource is of interest to you, and we’re always here to help if you have any questions about operator training.
Contact us on 01793 975353 or office@keyperformancetraining.co.uk for more information about how we can help or to book your course today.
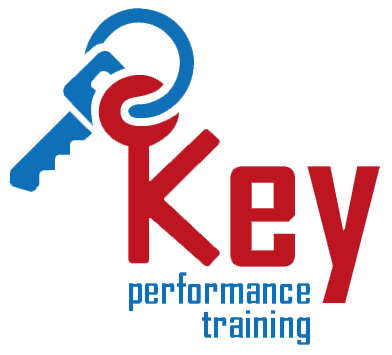
Need more information?
For more information please do get in touch.
You can reach us via our contacts page, via email or just give us a call on 01793 975353