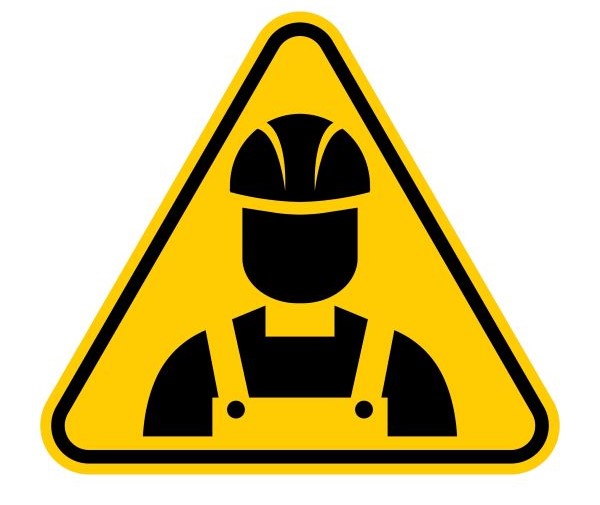
HSE Work Related Fatality Figures Released
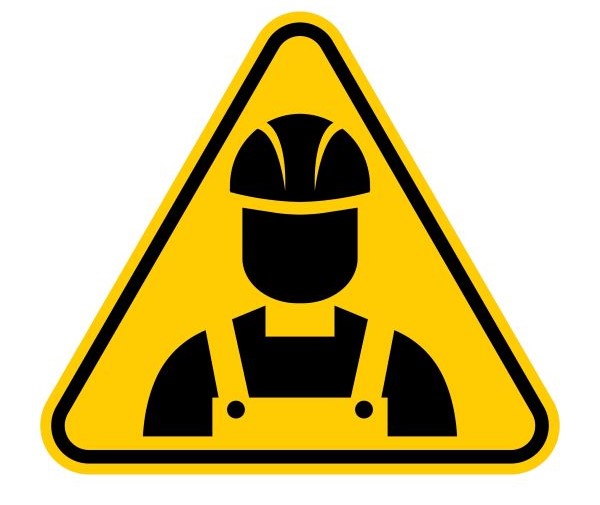
HSE WORK RELATED FATALITY FIGURES RELEASED
The HSE has recently published the figures for work related fatalities in the UK for the period April 2022 – March 2023.
Sadly, 135 workers were killed during this period, with the highest number of deaths in the construction industry (45), with agriculture, forestry, and fishing (21), manufacturing (15), and transportation and storage (15). Agriculture, forestry, and fishing has the highest rate of fatal injury per 100,000 workers of all the main industrial sectors followed by waste and recycling.

The three most common causes of fatal injuries are falls from height (40), being struck by a moving object (29), and being struck by a moving vehicle (20).
The total of 135 worker deaths in 2022/23 is higher than the previous year (123) but is in line with pre-pandemic levels. The figure for 2020/21 was 145.
Great Britain is one of the safest places in the world to work. There has been a long-term downward trend in the rate of fatal injuries to workers, though in the years prior to the coronavirus pandemic the rate was broadly flat.
A further 68 members of the public were killed following a work-related incident in 2022/23. This is a decrease of 20 from last year.
HSE’s Chief Executive Sarah Albon said: “Any loss of life in the workplace is a tragedy.
“While these figures show Great Britain is one of the safest countries in the world to work, safety must continue to be at the top of everyone’s agenda.
“Our mission is to protect people and places and we remain committed to maintaining safe workplaces and holding employers to account for their actions.”
The best way to ensure the safety of your employee’s is with regulated, high quality training, which is compliant with the HSE rules, guidance and legal obligations.
To view our range of courses, please see https://keyperformancetraining.co.uk/courses/
Contact us on 01793 975353 or rachel.gearon@keyperformancetraining.co.uk for more information about how we can help or to book your course today.
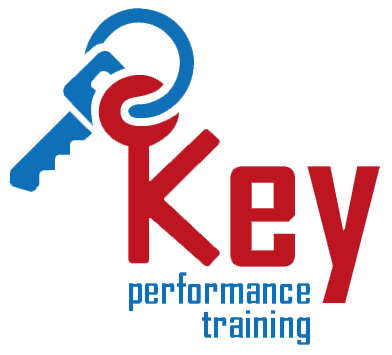
Need more information?
For more information please do get in touch – via our contacts page, email us or just give us a call on 01793 975353